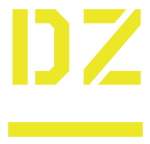
DOCKZILLA MAINTAINS COLD SHIPPING OPERATIONS DURING CONSTRUCTION
As part of a long-term renovation project to modernize its pork processing plant in Fremont, NE, Wholestone Farms tapped Dockzilla for a temporary modular building extension to their existing warehouse.
The company needed to maintain its cold storage shipping & receiving operations during warehouse construction, keeping them fully operational during a three-year renovation project without the significant investment, lead time, or permanence involved with stick-built construction.
Dockzilla combined its expertise in loading docks and logistics with modular construction concepts to connect a 7,376 sq ft refrigerated “temp-dock” facility to Wholestone Farms’ warehouse. The company plans to utilize their modular distribution center during the construction period, then eventually relocate their investment elsewhere on the property when construction wraps.
Project Specs:
- Built-to-spec design using modular building extension, pre-engineered to integrate with existing facility
- Temperature controlled with refrigeration for integrity of food shipments
- 10 dock-height loading docks to service standard trailers
- Installed in a matter of weeks
KEEP SHIPPING & RECEIVING FULLY OPERATIONAL DURING CONSTRUCTION
Wholestone Farms faced the challenge of replicating their existing cold storage loading & unloading during the warehouse’s three-year renovation. Traditional stick-built construction was not a viable option. It would have been:
- Costly: Traditional construction methods can be expensive, exceeding budget limitations for a temporary solution.
- Time-Consuming: Construction timelines wouldn’t align with Wholestone Farms’ need for a swift solution to minimize disruption.
- Unnecessary Permanence: Building a permanent addition wouldn’t be practical since the need was temporary.
The Solution
Modular Marvel: Relocated Shipping & Receiving with Temporary Modular Warehouse
Dockzilla stepped up with a unique approach – a temporary, modular building extension. This 7,376 sq. ft. temperature-controlled “temp-dock” seamlessly integrated with Wholestone Farms’ existing warehouse. Built to precise specifications, the modular extension featured:
Seamless, Elevated Platform
The customized configuration utilized 37 self-supported, steel platform sections that kitted together to form an elevated foundation. Cross-bracing and adjustable base plate footing supported the platform to handle daily loading dynamics such as forklift and trailer impact.
10 Dock-Height Loading Docks
The platform featured self-supported dock levelers installed on the exterior of the structure. This enables the dock door to close directly the building floor, while the shelter forms a seal around the truck during loading and unloading, to save energy while maintaining the building’s temperature.
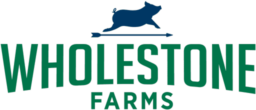
“Dockzilla’s ‘temp-docks’ are literally helping us bridge the gap between our current operations and the future state of our business. The modular shipping facility allows us to maintain business continuity during construction and eventually relocate the structure to maximize our investment. Dockzilla’s modular shipping facility concept has a significant advantage over stick-built construction due to velocity – their team had our new loading docks up and running in a few weeks.”
– Steven Weers, VP & GM of Operations, WholeStone Farms
The Results
Engineering Feats That Improve Efficiency
Dockzilla’s engineers incorporated a slight incline into the platform to address existing grade differences and integrated a steel transition plate for seamless movement between the permanent and temporary facilities. Additionally, the design connected previously segregated sections of the warehouse, streamlining forklift traffic patterns. The result? A significant boost in operational efficiency.
With Great Speed Comes Great Flexibility
Wholestone Farms bypassed traditional construction headaches with Dockzilla’s pre-fab solution which went from delivery to operation in record time.
But the benefits didn’t stop there. This modular unit is built for flexibility, giving Wholestone Farms the freedom to relocate it anywhere, ensuring they can leverage their investment for years to come.
No Time for Downtime
Dockzilla pulled off a logistical feat by helping Wholestone Farms maintain uninterrupted cold shipping and receiving throughout their three-year warehouse renovation project. This wasn’t just about keeping the lights on; it’s about millions of dollars of perishable goods and the trust of their customers.
Ask an Engineer
Stop shopping and talk to a real engineer who understands what goes down at the loading dock.