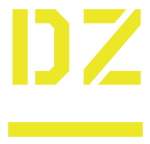
DOCKZILLA DOCK HOUSE RETROFIT DRIVES SUSTAINABILITY & SAVINGS AT LEASED FACILITY
A European global logistics leader sought Dockzilla’s expertise, as they expand in the U.S., to convert a leased warehouse into an energy efficient first-mile loading hub.
With sustainability at the forefront of their decision-making, they employed Dockzilla to install 44 Dock House-style dock levelers to leverage this exterior, bolt-on design. By attaching levelers to the outside of the facility, they avoided the construction process involved with installing pit-style levelers, and negated energy-zapping air gaps that occur when the building floor is excavated for antiquated pit levelers.
The Dock House design allows the door to close tightly on the concrete floor vs a steel dock plate, resulting in substantial annual energy savings.
Results at a Glance:
- 44 exterior, modular Dockzilla Dock Levelers with Dock Houses attached to leased facility
- Anticipated energy savings of ~$19k annually
- Application-specific sizing to accommodate varied vehicle sizes and capacities
- Gained 4,400 square feet (100 sq ft/per dock) of usable indoor floor space
- Ability to remove and relocate the Dock Houses when lease ends, savings thousands in reclamation costs
Modern & Sustainable Approach To Loading Dock Design
The customer, with a network of 1,600 facilities spanning 80+ countries, leased a new facility and needed to quickly kickstart a high velocity first-mile loading operation that would accommodate a variety of trailer sizes and freight capacity.
Beyond managing their continuous on-site loading, the customer was eager to find an energy-efficient docking solution that aligned with their company’s larger sustainability goals.
A “one size fits all” loading dock approach was not an option.
Project Must-Haves:
- Ability to accommodate several trailer varieties and capacities
- Energy-efficient solution that ladders up to broader sustainability initiative
- Speedy installation; docks up and running ASAP without major construction
- An asset that can be relocated once their building lease is up
The Solution
Collaborating closely with the customer, Dockzilla engineers proposed a custom solution, with a variety of Dock Levelers sizes with Dock Houses, to transform their facility into an energy-efficient loading hub.
The Results
~$19k in Energy Savings Annually
By installing 44 exterior, bolt-on Dock Levelers and Dock Houses, the customer slashed more than $1,500 per month from their energy bills (according to a Frontier Energy report), even in a mild California climate. They were able to demonstrate how warehouse operations can contribute to the company’s broader sustainability initiative.
Designed to Spec, Built to Move
The plan, inclusive of varying dock leveler sizes and capacities, was designed for the site’s loading needs. However, the modular, expandable Dock Levelers and Dock House are relocatable so the customer can leverage the assets if or when they move to another facility.
All-Inclusive Project Management, No Costly Down Time
Unlike internal pit-style dock levelers that require weeks of demolition and disruption for installation, the customer’s 44 Dock Levelers and Dock Houses were installed in under four weeks, with no internal disruption or mess from concrete silica dust due to pit construction. The entire process was managed by Dockzilla so the customer never had to coordinate hard-to-find tradespeople.
Ask an Engineer
Stop shopping and talk to a real engineer who understands what goes down at the loading dock.
Related Products
CROSS DOCKING PLATFORM
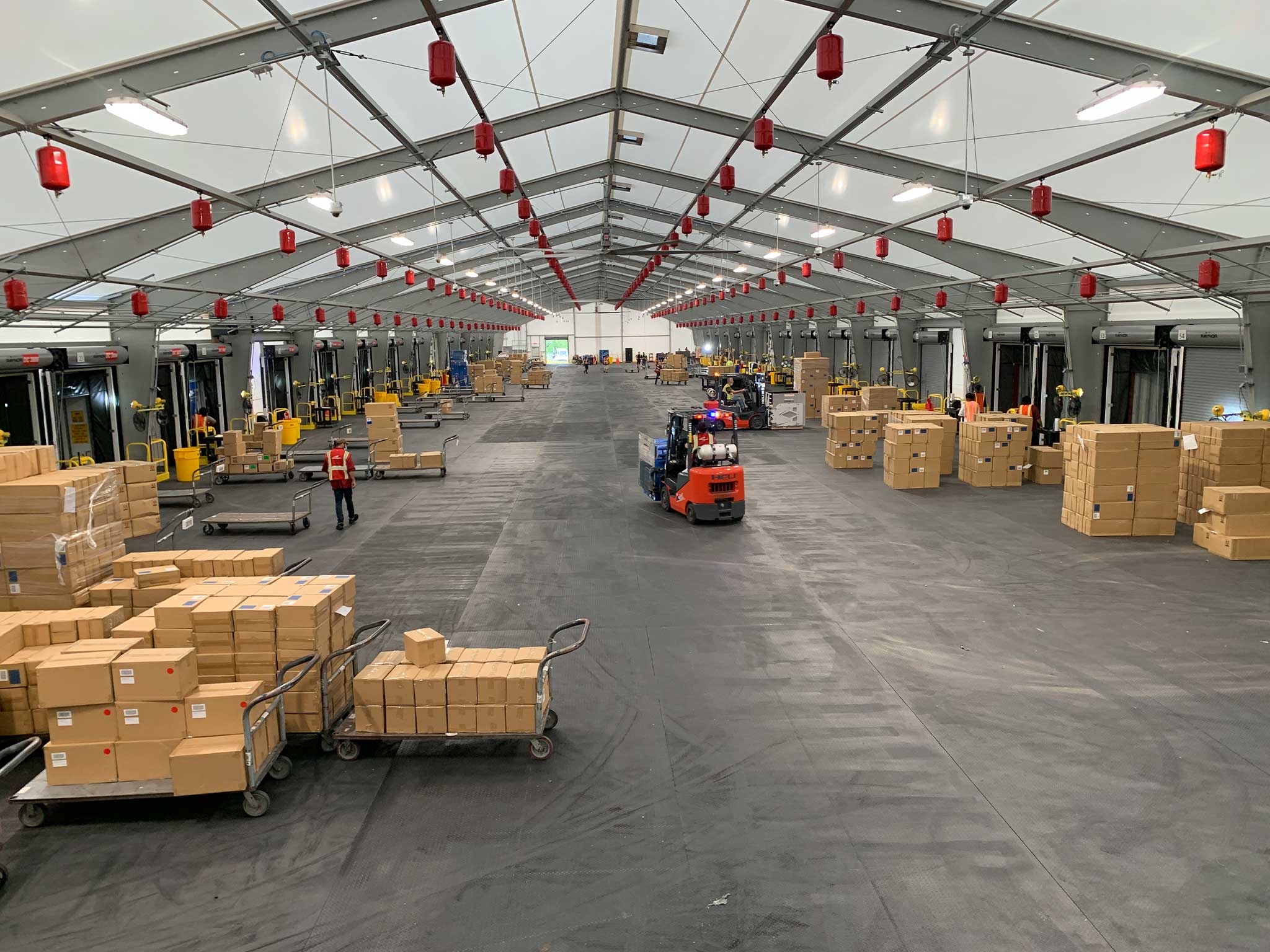
Dockzilla’s freestanding distribution platforms create high-speed cross docking and transloading capabilities on any property.
DISTRIBUTION WAREHOUSE
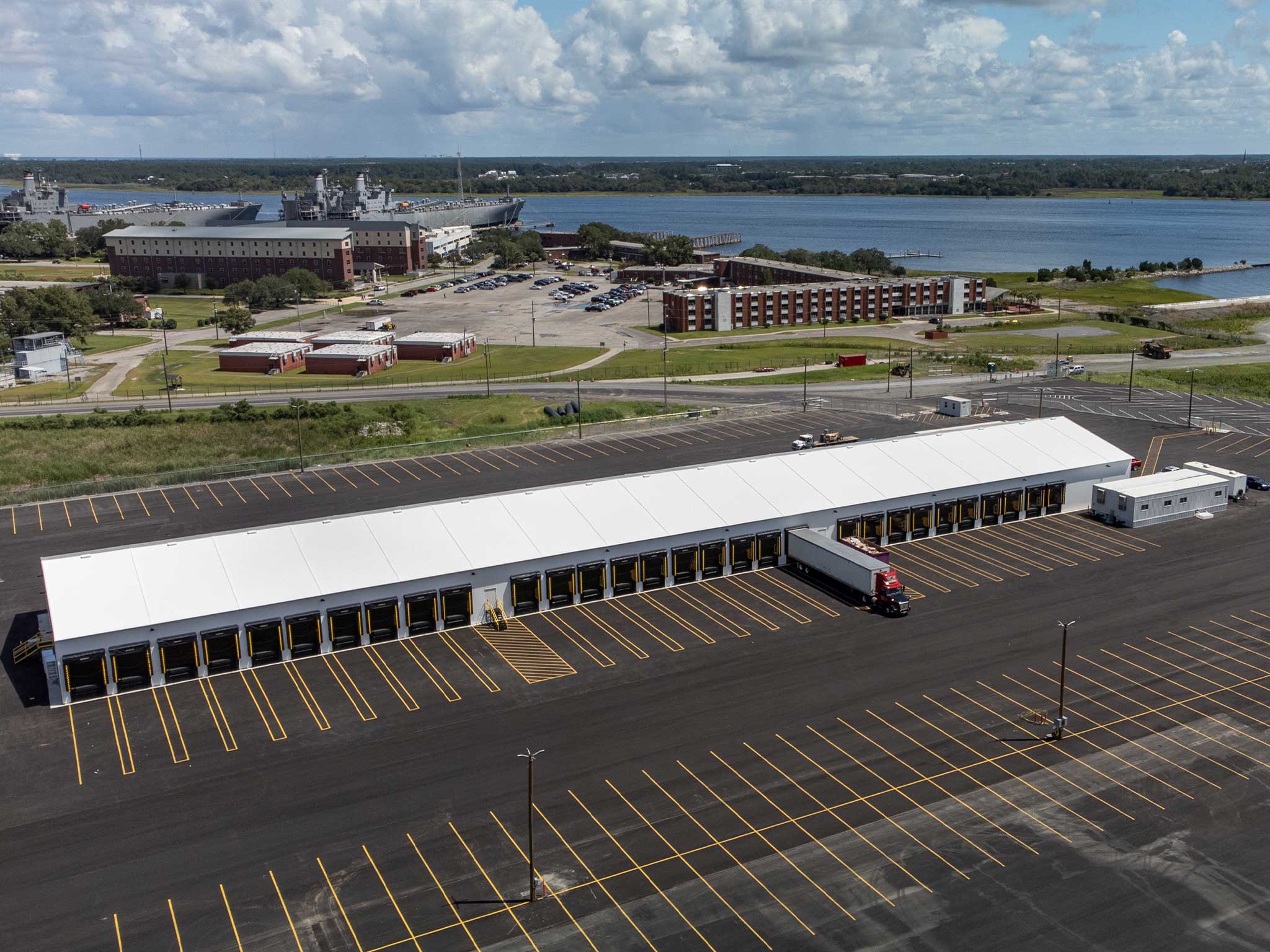
Dockzilla’s Distribution Warehouse combines modular buildings and loading dock equipment to stand up a high-speed fulfillment center and last-mile distribution anywhere needed.